- DIY misAdventures
- Posts
- Understanding Epoxy Cure Time: A Practical Guide
Understanding Epoxy Cure Time: A Practical Guide
Learn the ins and outs of epoxy cure times with this practical guide, offering tips on how to ensure your projects harden perfectly.
Epoxy cure time varies widely from 24 hours to several days. Temperature, hardener type, and epoxy volume affect this duration. This guide will help you understand and manage these factors for optimal results.

Key Takeaways
Epoxy cure time is influenced by factors like hardener speed, temperature, and the amount of epoxy used, which can affect the final product’s strength and appearance.
Different epoxy types have various curing characteristics. Epoxy cure times can range from a minimum of few hours to a maximum of several days, depending on the type and conditions.
For best results, beginners should start with small projects, carefully calculate epoxy needed, and prepare their workspace to avoid common issues like air bubbles and overheating.
Understanding Epoxy Cure Time: A Practical Guide
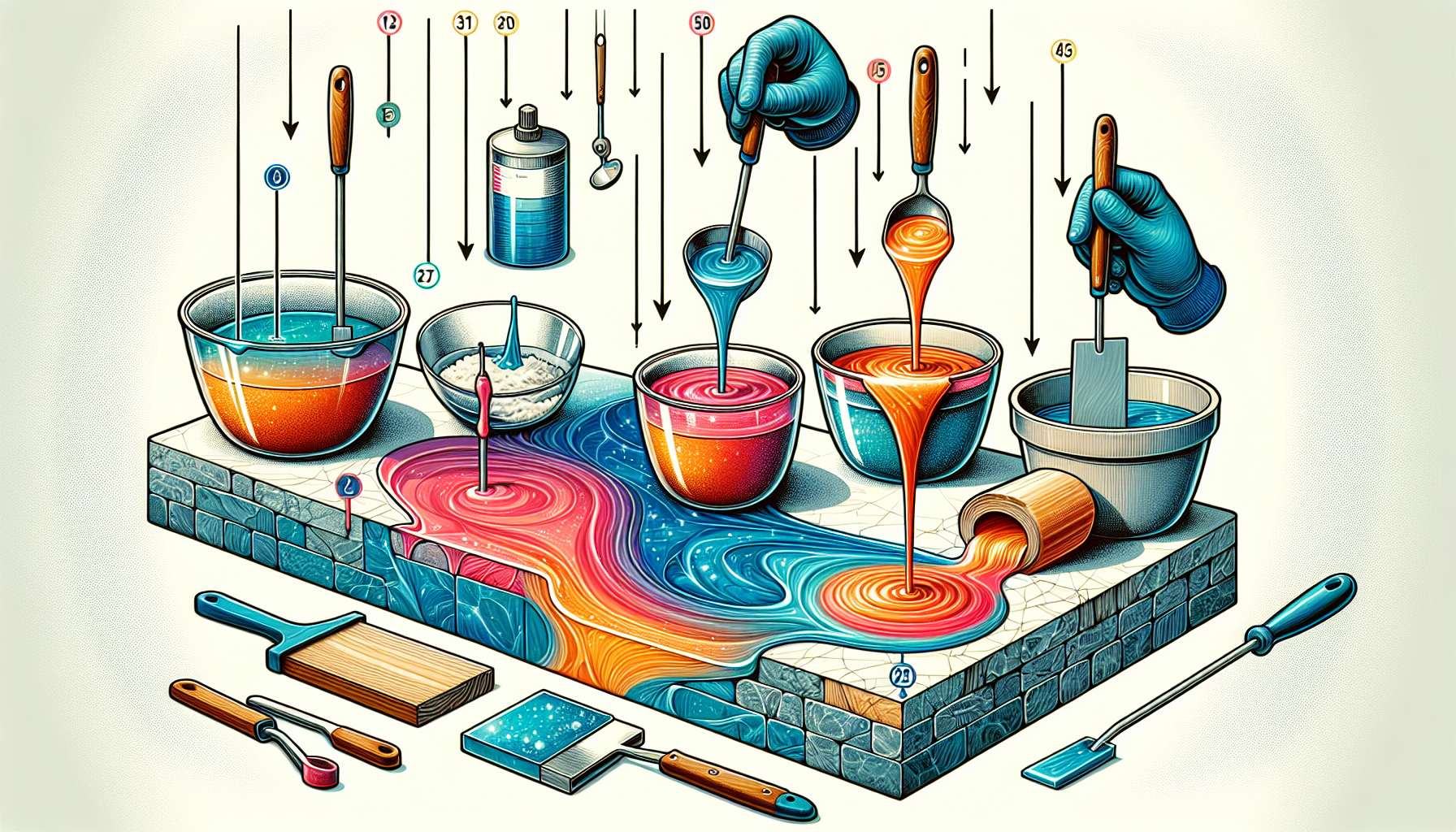
Epoxy resin curing time is more than just waiting for your project to dry; it’s a critical phase that dictates the final strength, appearance, and durability of your work. Factors like hardener cure speed, ambient temperature, epoxy resin drying times, and the volume of epoxy used all play a role in how quickly your epoxy cures.
For more practical information please refer to my previous blog posts:
Introduction
This guide will teach you how to optimize cured epoxy curing time, discuss factors that influence it, explore different types of epoxy resins, and offer techniques to manage the process.
Whether you’re a novice or a seasoned crafter, understanding these elements is key to achieving flawless results in your epoxy resin projects.
Understanding Epoxy Cure Time
Understanding epoxy cure time is crucial for creating durable and visually appealing resin projects. During curing, mixed epoxy transforms from a liquid to a gel and then into a solid. Temperature significantly affects this duration, and drying times vary based on epoxy type and environmental conditions.
Factors like the hardener’s cure speed and the epoxy temperature play a significant role in determining how quickly your epoxy cures. Using a fast-curing hardener or working in a warmer environment can speed up the process, while slower hardeners and cooler temperatures will extend the curing time.
This variability means you need to adjust your approach based on the specific requirements of your project.
Factors Influencing Epoxy Cure Time

Epoxy cure time depends on the hardener’s speed, ambient temperature, and exothermic heat generated during curing.
Understanding these elements can help you better manage the curing process and achieve the desired results.
Hardener Cure Speed
The type of hardener significantly impacts epoxy curing speed. Different formulations result in varying curing times, so always check product labels for pot life and curing time guidance.
Ambient Temperature
Ambient temperature also affects epoxy curing. A range of 20-24°C (68-75°F) is ideal for most resins. Higher temperatures speed up curing, while lower ones slow it down.
Humidity levels also play a minor role; high air humidity can cause issues if not managed properly.
Exothermic Heat Generated
Exothermic heat from the chemical reaction can speed up curing, especially in thicker masses. Careful management is essential to avoid defects.
The exothermic reaction is a chemical process where the epoxy resin and hardener react to form a solid material, releasing heat in the process. When the critical volume is exceeded, the heat generated will accelerate the reaction rate, causing the epoxy to cure too quickly. This rapid curing will trap air bubbles, create stress within the material, and lead to imperfections. Additionally, the excessive heat can cause the epoxy to discolor and even deform. Therefore, understanding and respecting the critical volume is crucial for maintaining the quality and integrity of your epoxy projects.
Significance of Full Volume Mixing
Careful mixing of epoxy resin and hardener is essential for a consistent and effective cure. If the components are not thoroughly mixed, you may end up with soft spots, uneven curing, and a weaker final product. To avoid these issues, always mix the resin and hardener in the exact recommended ratio. Be sure to scrape the sides and bottom of your mixing container to incorporate all the material. Properly mixed epoxy ensures an uniform blend, resulting in a strong and flawless finish for your project.
Follow strictly mixing instructions.
Types of Epoxy Resins and Their Cure Times
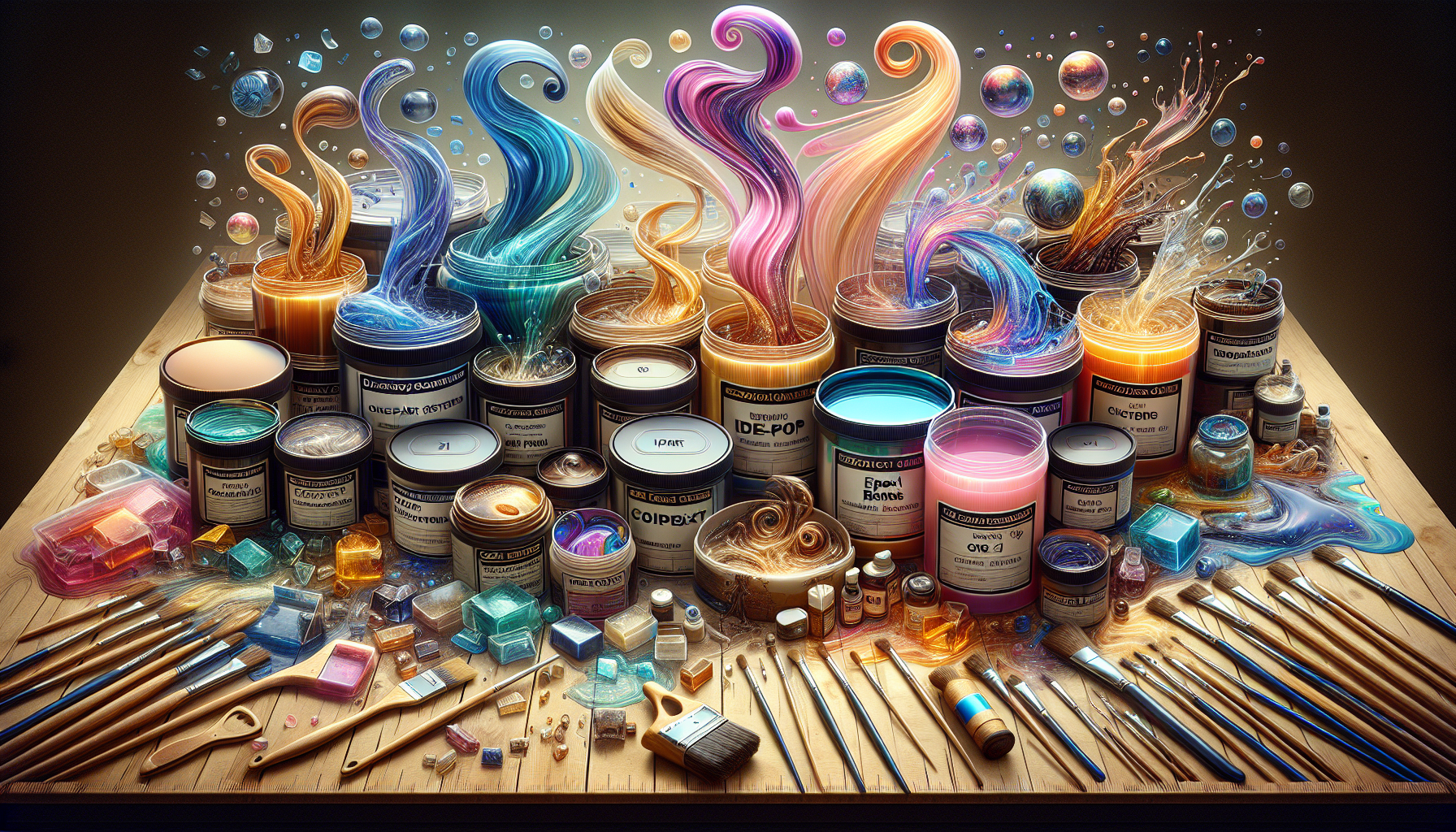
Epoxy resins have various formulations, each with unique curing characteristics. They are generally categorized into one-part and two-part systems.
The choice of resin and hardener significantly affects the overall curing time.
One-part Epoxy Systems
One-part epoxy systems are easier to apply because they don’t require mixing but usually need heat activation. They typically need to be heated to 125°C to 150°C and cure more slowly than two-part systems.
UV Resins
UV resin is example of one-part system curing quickly when exposed to ultraviolet light. It’s ideal for small projects and intricate designs, as it allows for precise control and rapid curing. UV resin is often used in jewelry making, crafts, and small repairs due to its convenience and fast curing time.
Two-part Epoxy Systems
Two-part epoxy systems involve mixing a resin and a curing agent to start the curing process. Curing time varies from 24 hours to several days, depending on the product and conditions.
Types of Two-part Epoxy Systems
Two-part epoxy systems involve mixing a resin and a curing agent to start the curing process. Curing time varies from 24 hours to several days, depending on the product and conditions. These two-part epoxy systems offer a range of properties tailored to specific applications, ensuring optimal performance and results for your projects.
Here are some common types of two-part epoxy systems available in the market:
Table Top Epoxy
Known for its high-gloss finish and durability, table top epoxy is often used for furniture and countertops. It typically needs at least 72 hours to cure fully.
Art Epoxy
Art epoxy is designed for creative projects like resin art, jewelry, and crafts. It offers a clear, glossy finish and is formulated to minimize bubbles and imperfections, making it ideal for intricate designs.
Boat Epoxy
Boat epoxy is specifically formulated for marine applications. It provides excellent water resistance, durability, and strength, making it suitable for boat repairs and construction.
Casting Epoxy
Casting epoxy is used for creating molds, sculptures, and other deep-pour projects. It cures slowly to allow for thicker pours without overheating and is often used in river tables and other large castings.
Flooring Epoxy
Flooring epoxy is designed for use on concrete floors in garages, basements, and industrial settings. It provides a durable, chemical-resistant surface that can withstand heavy traffic and wear.
Techniques to Control Epoxy Cure Time

Several techniques can control the epoxy curing process, such as using slow or fast hardeners, adjusting ambient temperature, and adding supplemental heat. Proper preparation and understanding product instructions are crucial for optimal results in curing epoxy.
Using Slow or Fast Hardeners
Using the correct mix ratio is vital; incorrect ratios can cause soft or sticky epoxy. Slow hardeners suit warm conditions, while fast hardeners work best in cooler environments.
Adjusting Ambient Temperature
An optimal temperature range of 24°C to 27°C (75°F to 80°F) can significantly affect curing time, with warmer conditions facilitating faster reactions within the ideal temperature cure range and room temperature curing.
However, be mindful of potential bubble formation due to out-gassing when heating epoxy on porous surfaces.
Additional Heat
Using heat lamps or heating blankets can accelerate curing. These methods enhance exothermic heat, leading to faster and more uniform results.
While adding supplemental heat can accelerate the epoxy curing process, it also comes with certain risks that must be carefully managed.
Risk of Overheating
Excessive heat can cause the epoxy to cure too quickly, leading to defects such as bubbles, cracks, and discoloration. This rapid curing can also trap air within the epoxy, resulting in a compromised finish and reduced structural integrity. To mitigate this, always monitor the temperature closely and avoid exceeding the recommended heat levels.
Uneven Curing
Inconsistent application of heat can lead to uneven curing, where some parts of the epoxy may harden faster than others. This can create stress within the material, causing it to warp or crack over time. To avoid this, apply heat uniformly across the surface and use tools designed for even heat distribution.
Health Risks
Prolonged exposure to high temperatures can release harmful fumes from the epoxy. Always work in a well-ventilated area and use appropriate personal protective equipment (PPE) such as masks and gloves to minimize inhalation risks. Additionally, follow manufacturer guidelines for safe handling and curing practices.
By understanding and managing these additional heat risks, you can ensure a safer and more successful epoxy curing process.
Post-Curing for Enhanced Properties
Post-curing enhances epoxy’s physical properties, increasing strength and durability. Maintaining a safe maximum temperature of 49°C (120°F) during post-curing avoids defects like yellowing or cracking. Applying heat can significantly strengthen the epoxy.
After pouring epoxy into a mold, allow it to level and release air bubbles.
Avoid removing the form until the epoxy is fully cured.
Common Issues and Solutions During Curing
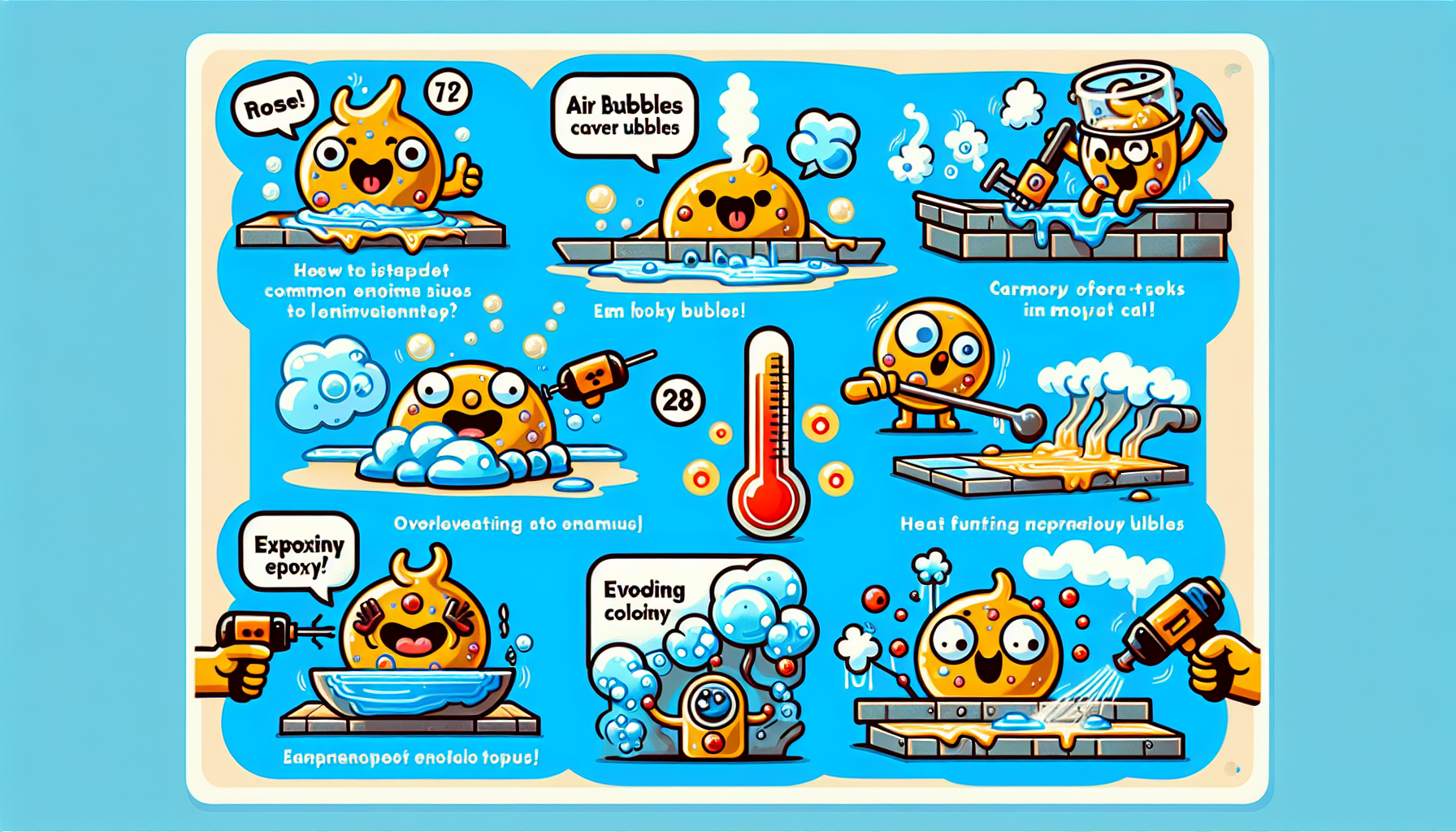
Common issues during epoxy curing include air bubbles, overheating, and improper mixing. Managing these problems ensures a flawless finish.
Dealing with Air Bubbles
Air bubbles can result from trapped air in porous substrates or improper mixing. Using a heat gun or propane torch can effectively eliminate them shortly after pouring.
Applying a seal coat on porous surfaces can prevent bubbles from forming as the wood off-gasses during curing.
Preventing Overheating
Managing the exothermic reaction is crucial to avoid overheating. Pouring epoxy into a shallow container helps dissipate heat and prevents overheating.
Ensuring Proper Mixing
Thoroughly mixing both epoxy components is vital to avoid soft spots and achieve a consistent cure. Mix resin and hardener in the exact recommended ratio to ensure a homogeneous mixture.
Practical Tips for Beginners
Beginners should start with small projects to build confidence and skills with epoxy resin. Calculating the needed epoxy and properly preparing your workspace are crucial steps for success.
Starting Small
Beginners should start with simple projects like serving trays or small inlays to gain hands-on experience without significant risk.
Calculating Epoxy Quantity
Determine the amount of epoxy resin needed by multiplying the length, width, and height of the project. For even more accurate measurements, consider using online volume calculators specifically designed for epoxy resin projects. These tools can help you avoid miscalculations and ensure you have the right amount of epoxy for your project.
Order extra epoxy to account for spillage or miscalculations during mixing.
Preparing Your Workspace
Ensure your workspace is flat and covered to prevent leaks. Maintain an organized area to enhance efficiency during application, and cover surfaces with protective materials to avoid damage from spills.
Summary
Understanding and managing epoxy cure time is essential for successful resin projects. By considering factors like hardener cure speed, ambient temperature, and exothermic heat, and by applying practical techniques and tips, you can achieve optimal results. Now, with this knowledge, you’re ready to tackle your epoxy projects with confidence.
Frequently Asked Questions
What is the recommended starting project size for beginners in epoxy casting?
Starting with small projects like serving trays or inlays is your best bet as a beginner in epoxy casting. It keeps things manageable and lets you build your skills without overwhelming yourself.
How should one calculate the amount of epoxy resin needed for a project?
To figure out how much epoxy resin you need, calculate the volume of your project in liters or gallons, then order at least 10% extra to account for any shrinkage. Better to have a little more than to run out!
What properties should be considered when selecting epoxy for casting?
When picking epoxy for casting, definitely check the maximum cast thickness, mix volume, processing time, and hardening time. These factors will help ensure your project turns out just right.
What can happen if the casting/thickness ratio is not respected during epoxy casting?
If you ignore the casting/thickness ratio with epoxy, you might trigger an exothermic reaction that can heat things up fast and ruin your project. So, it's super important to stick to the ratio and mixing instructions.
What is a crucial preparation tip for casting with epoxy?
A crucial tip for casting with epoxy is to make sure your workbench is flat and covered with plastic wrap or tin foil to catch any leaks. This simple step can save you from a sticky mess!
Reply